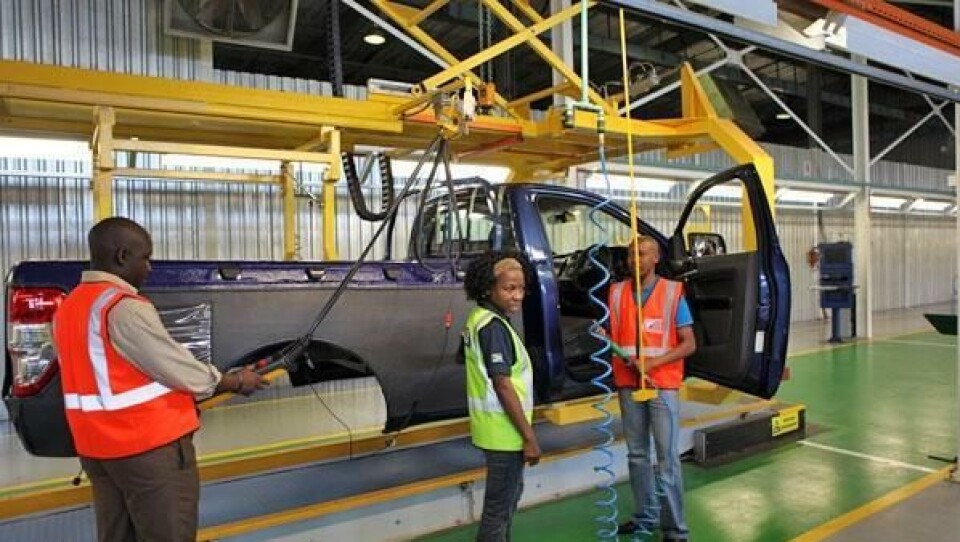
Her lages vinner-bilen
JOHANNESBURG (AT.no): Vi besøkte Ford Ranger-fabrikken.
Denne artikkelen ble publisert for over 10 år siden.
Mandag kveld vant Ford Ranger den prestisjetunge International Pick-Up Award under en seremoni i Dublin.
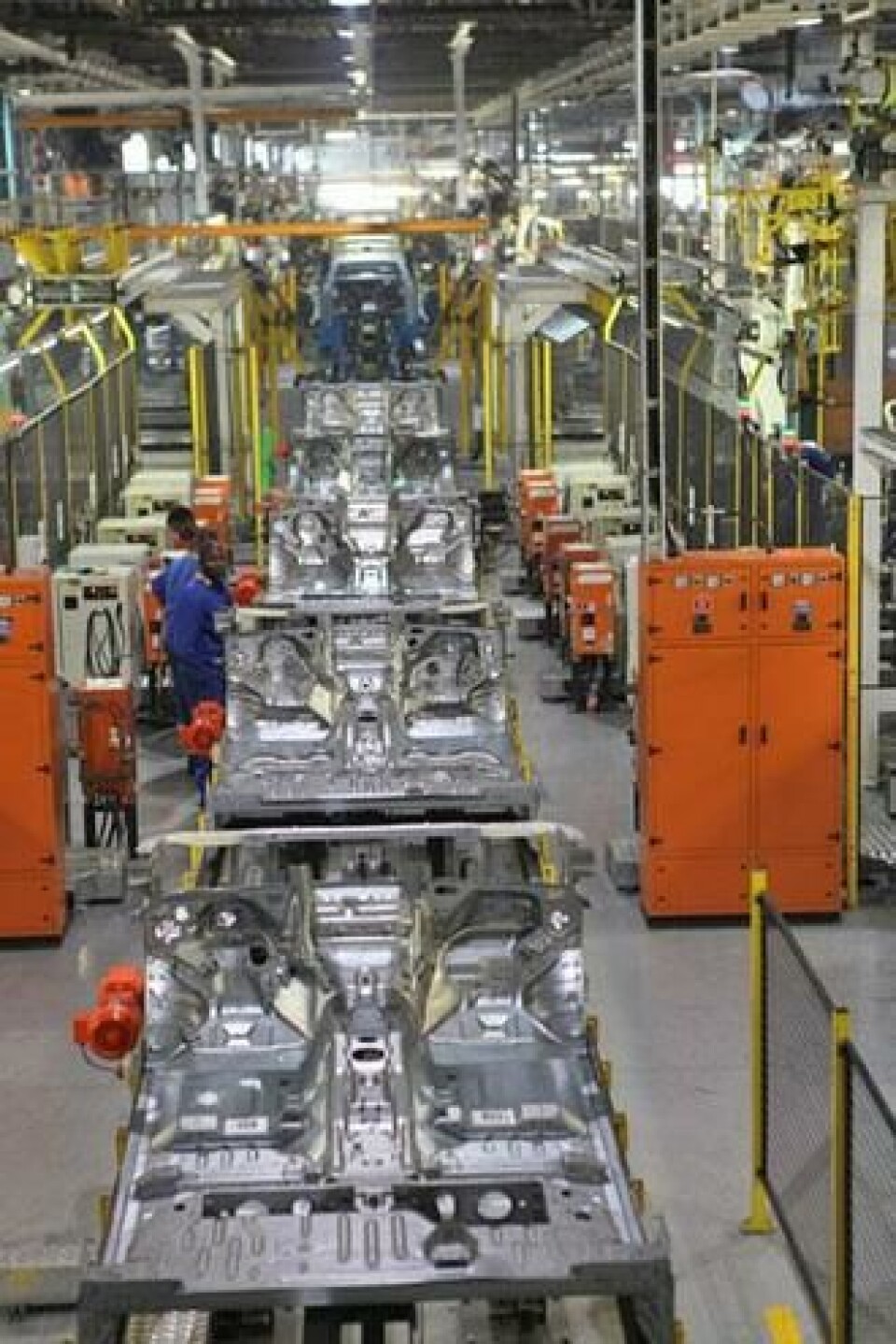
Les også:
Nye Ford Ranger/Mazda BT 50 blir produsert ved tre forskjellige fabrikker, fabrikkene i Sør Afrika og Argentina er under Fords ledelse Den siste fabrikken, AutoAlliance Thailand eies 50/50 av Ford og Mazda. For et drøyt år siden var AT.no på plass i fabrikken som ligger utenfor Johannesburg.
Ifølge Tim Day, produksjonssjef ved Fabrikken i Silverton, Sør Afrika, og ansvarlig for å innføre OneFord-konseptet der, er kvalitetsprodukter det viktigste hjelpemiddelet for å ha en høy produksjonskapasitet. Dersom man er nødt til å bruke tid og ressurser på å rette feil, vil fokuset endres fra produksjon til reparasjon, og færre biler blir produsert.
68% forbedring
Produksjonskvaliteten ved fabrikken er 68% bedre etter omorganiseringen. Et av de første punktene var å forbedre samholdet mellom arbeiderene, samt å sørge for et bedre eierforhold til produktene som produseres. Noen av punktene som ble gjennomført ved fabrikken var:
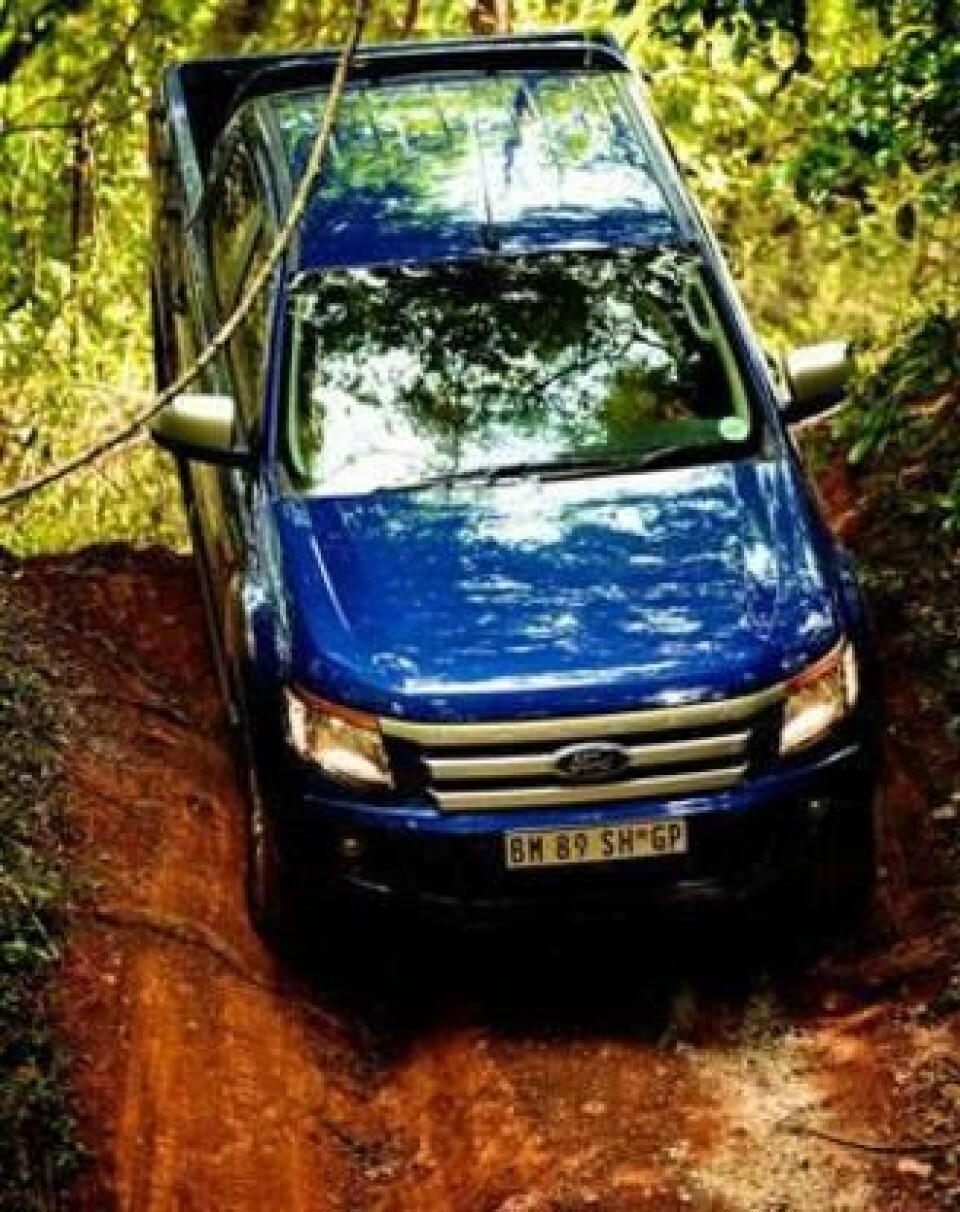
•Ford sendte 200 produksjonsledere på kurs i India
• 8 ingeniører hospiterte i 18 måneder ved Ford-fabrikker i USA.
• Alle fabrikkens arbeidere ble inndelt i team på 15-20 personer
• Produksjonslederne har ansvar for å etterutdanne sine egne medarbeidere i henhold til en 5-trinns plan i samarbeid med tre "Spesial-lærere".
• En egen opplæringshall hvor alle funksjoner på samlebåndet kunne simuleres, ble installert. Denne ble bygd med støtte fra myndighetene, som ser viktigheten av at arbeiderene får videreutdanning.
• Antallet DC-Tools(Digitalt styrte verktøy) ble økt fra 10 til 168. Verktøyet sørger for at alle skruer blir festet med riktig moment, riktig antall omdreininger og at samtlige bolter i syklusen blir festet. Arbeiderne fikk også grundig opplæring slik at de forsto nytten av verktøyene.
• På eget initiativ innførte arbeiderne 5 minutter med obligatorisk morgengymnastikk før arbeidsdagen starter.
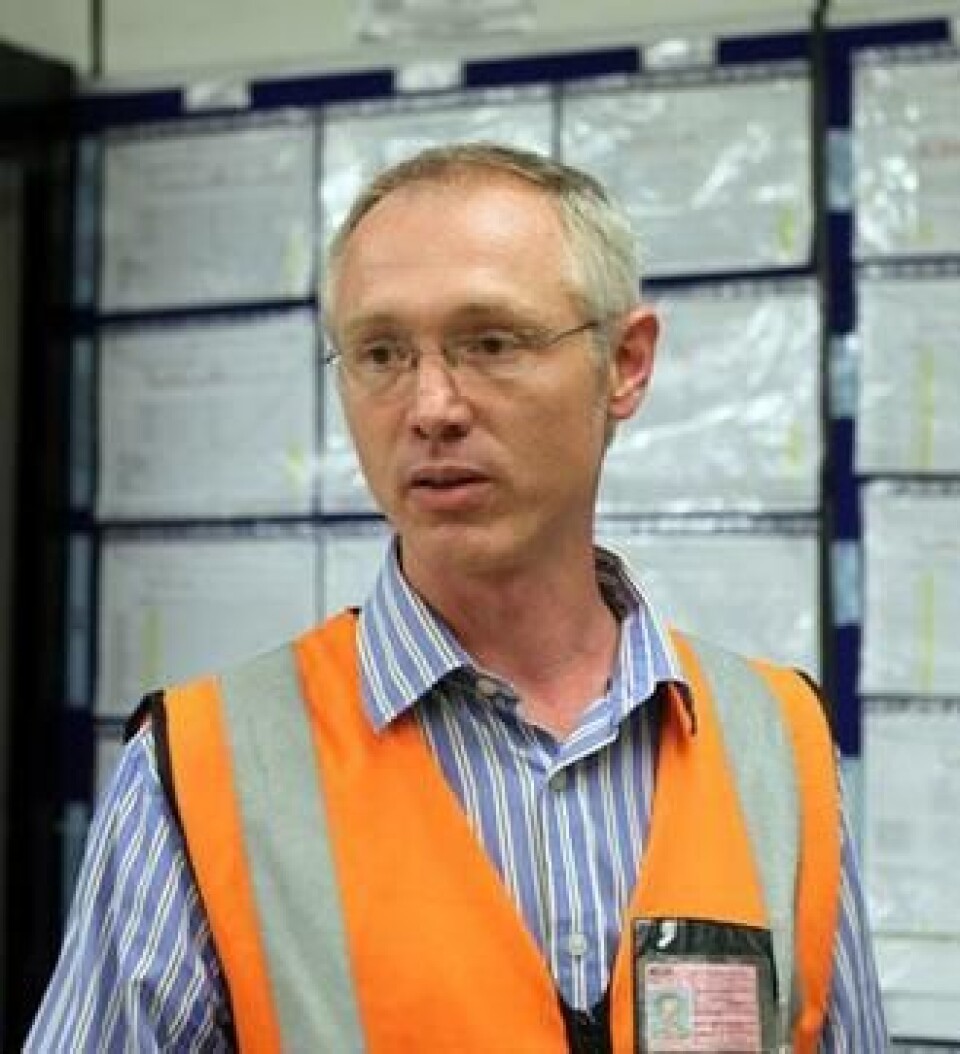
Sist, men ikke minst, ble antallet underleverandører betraktelig redusert slik at alle skulle ha et bredt nok økonomisk grunnlag til å kunne investere i kvalitet. I dag er det kun 60 lokale underleverandører mot over det dobbelte tidligere.
Resultatene viste seg allerede under produksjonen av forrige generasjon Ranger hvor kvaliteten på produktene oppnådde en forbedring på hele 68%.
Produksjonsmål
Da A&T besøkte fabrikken sist høst, var produksjonstakten kun 30-biler om dagen, men i løpet de påfølgende ukene skulle takten økes for å kunne produsere 110.000 biler i året. 75% av disse eksporteres til 148 land i Europa og Afrika.
Noen uker etter at AT.no var på besøk, ble fabrikken i Thailand rammet av store oversvømmelser. Dette førte også til en lengre produksjonsstans i Sør-Afrika, da én kritisk metalldel kun ble produsert ved denne fabrikken. Grunnet flommen i Thailand ble derfor Ranger introdusert flere måneder senere enn planlagt. I Norge var bilen først på plass rett før sommerferien.